INTEGASA nearly 50 years of experience in the field of S&T heat exchangers.
Supplier of NH3/CO2 cascade spray chillers for the food distribution industry that we integrate from our partner’s P&ID into a single unit with CE marking.
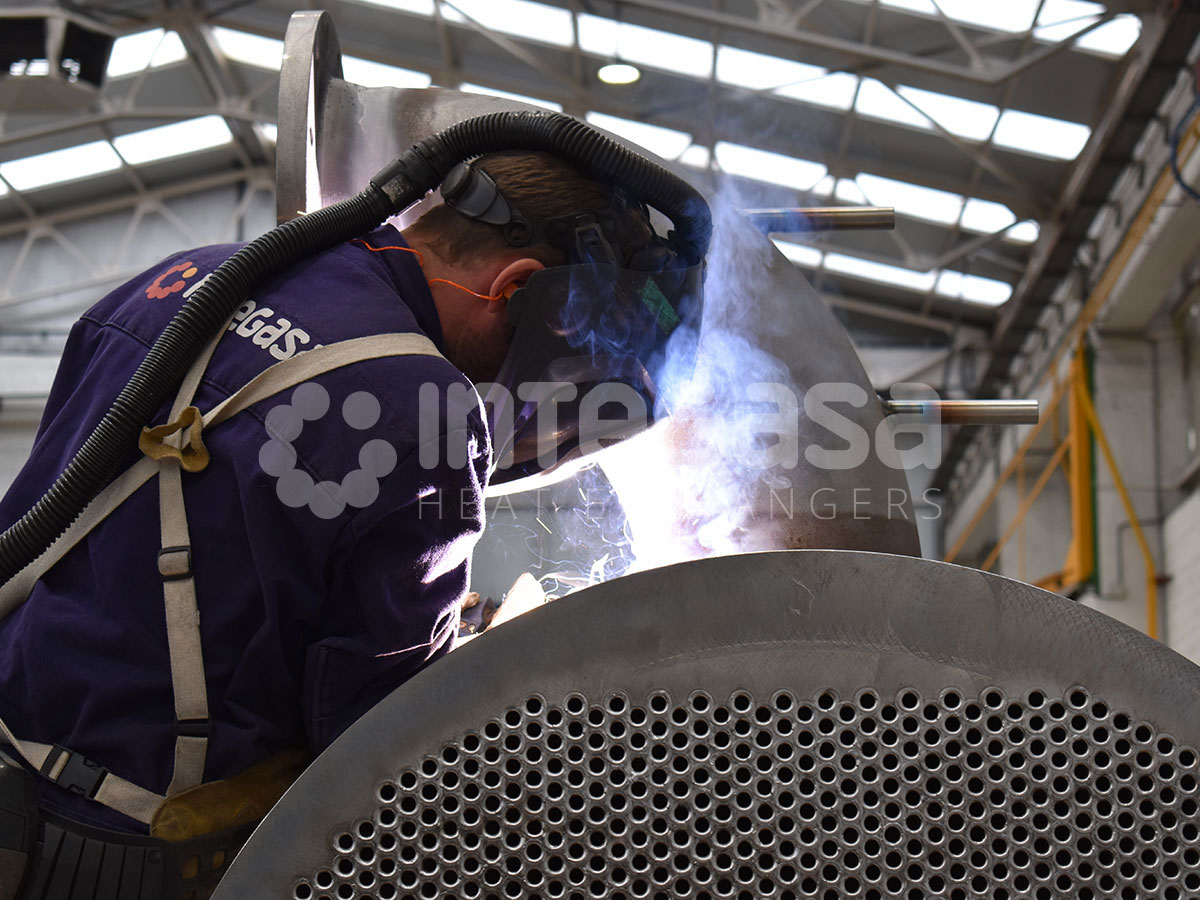
MANUFACTURING AND WELDING
INTEGASA is a reliable partner for developing projects for technical specifications demanding environments. Our company has become over the last several years a trusted and reliable equipment supplier for worldwide chemical, petrochemical, nuclear or marine sectors. Our goal is to design and manufacture customized solutions for specific needs.
We have widely demonstrated experience and we are recognized around the world because of the high technology and quality of our products and innovative and flexible processes.
We work according to the highest quality standards and norms and requirements of our clients developing new manufacturing process to keep us at the forefront of technology through our R+D projects.
WELDING
INTEGASA is certified under EN-ISO 3834-2 Standard: quality requirements for fusion welding of metallic materials and we weld with the most suitable technologies:
- Submerged arc welding SAW
- Gas Tungsten arc welding GTAW
- Semi automatic welding: GMAW, FCAW
- Manual: SMAW
- Orbital welding (GTAW) with and without filler metal
- Brazing
The main materials INTEGASA works with both for welding and weld overlay are:
- Carbon Steel (CS)
- Stainless Steel
- CuNi
- Duplex & superduplex Steel
- Titanium…
To join tubes and tube plate, we select the best technology for the project:
- Expanded
- Welded
- Expanded and welded
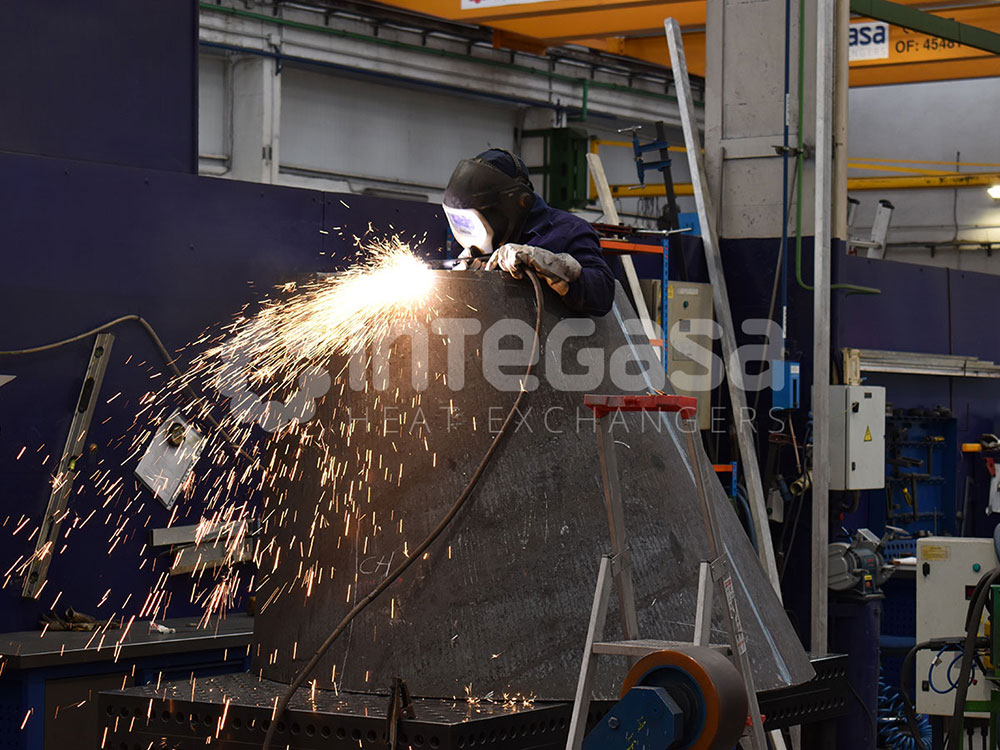
For the tube to tube-plate welding INTEGASA uses orbital welding Hot /Cold Wire TIG welding, this allows us to weld difficult materials such as titanium, duplex, zirconium, aluminum…
In this automated process, the welding tool is automatically rotated 360º around the tube. It solves problems of operator errors and allows a uniform sealed welding around tubes with the best quality. Because orbital welding is performed in an inert atmosphere, results are very clean and avoids unwanted spatter.
Orbital welding allows an increased productivity, consistent weld quality for each project and improved safety for our workers.
The system includes a programmable power supply with an integrated computer control that allows to set a range of different parameters (current intensity, pulse rate, flow of shielding gas, welding head rotating speed and wire feed options). INTEGASA uses different orbital welding heads according to the project, each of them holds the electrode in place, manage the flow of the welding current and controls the temperature.
When a new welding procedure is needed to join tubes and tube plate, a mock up is carefully prepared and tested at a certified laboratory.
For the welding of the shells, usually in longitudinal and circumferential butt welds (that are carried in the flat position thanks to a turning device), INTEGASA uses mainly automated Submerged-Arc Welding (SAW), this process involves the formation of an arc between a continuously fed electrode and the shell. The protective gas and the slag which protects the weld zone is generated by a blanket of powdered flux covering the welding joint (therefore shielding gas is not required).
Fluxes used by INTEGASA includes oxides of manganese, silicon, titanium, aluminium, zirconium, magnesium and other compounds. It is specially formulated to be compatible with the specific welding procedure used in the project.
As the arc moves along the joint line, excess flux is recycled via a hopper. Remaining fused slag layers can be easily removed after welding. Parameter setting like welding current, arc voltage and travel speeds and positioning of the filler wire affect bead shape, depth of penetration and chemical composition of the deposited weld metal.
As the arc is completely covered by the flux layer, heat loss is extremely low (at least half than with manual metal arc) and there is no visible arc light, process is spatter-free and there is no need for fume extraction ensuring a safe environment.